Alcast Company Can Be Fun For Anyone
Alcast Company Can Be Fun For Anyone
Blog Article
An Unbiased View of Alcast Company
Table of ContentsFacts About Alcast Company RevealedSome Known Details About Alcast Company Not known Details About Alcast Company The Best Guide To Alcast CompanyNot known Incorrect Statements About Alcast Company Alcast Company - The Facts
The refined difference exists in the chemical material. Chemical Contrast of Cast Aluminum Alloys Silicon promotes castability by minimizing the alloy's melting temperature level and improving fluidness during casting. It plays a critical duty in permitting detailed molds to be filled up accurately. In addition, silicon adds to the alloy's stamina and wear resistance, making it useful in applications where resilience is essential, such as vehicle parts and engine components.It also improves the machinability of the alloy, making it much easier to refine into ended up products. In this way, iron adds to the general workability of light weight aluminum alloys.
Manganese adds to the strength of aluminum alloys and boosts workability. Magnesium is a light-weight element that supplies strength and impact resistance to aluminum alloys.
Alcast Company - Truths
Zinc enhances the castability of light weight aluminum alloys and assists control the solidification process during casting. It improves the alloy's stamina and hardness.

The main thermal conductivity, tensile strength, yield stamina, and prolongation vary. Among the above alloys, A356 has the greatest thermal conductivity, and A380 and ADC12 have the cheapest.
An Unbiased View of Alcast Company
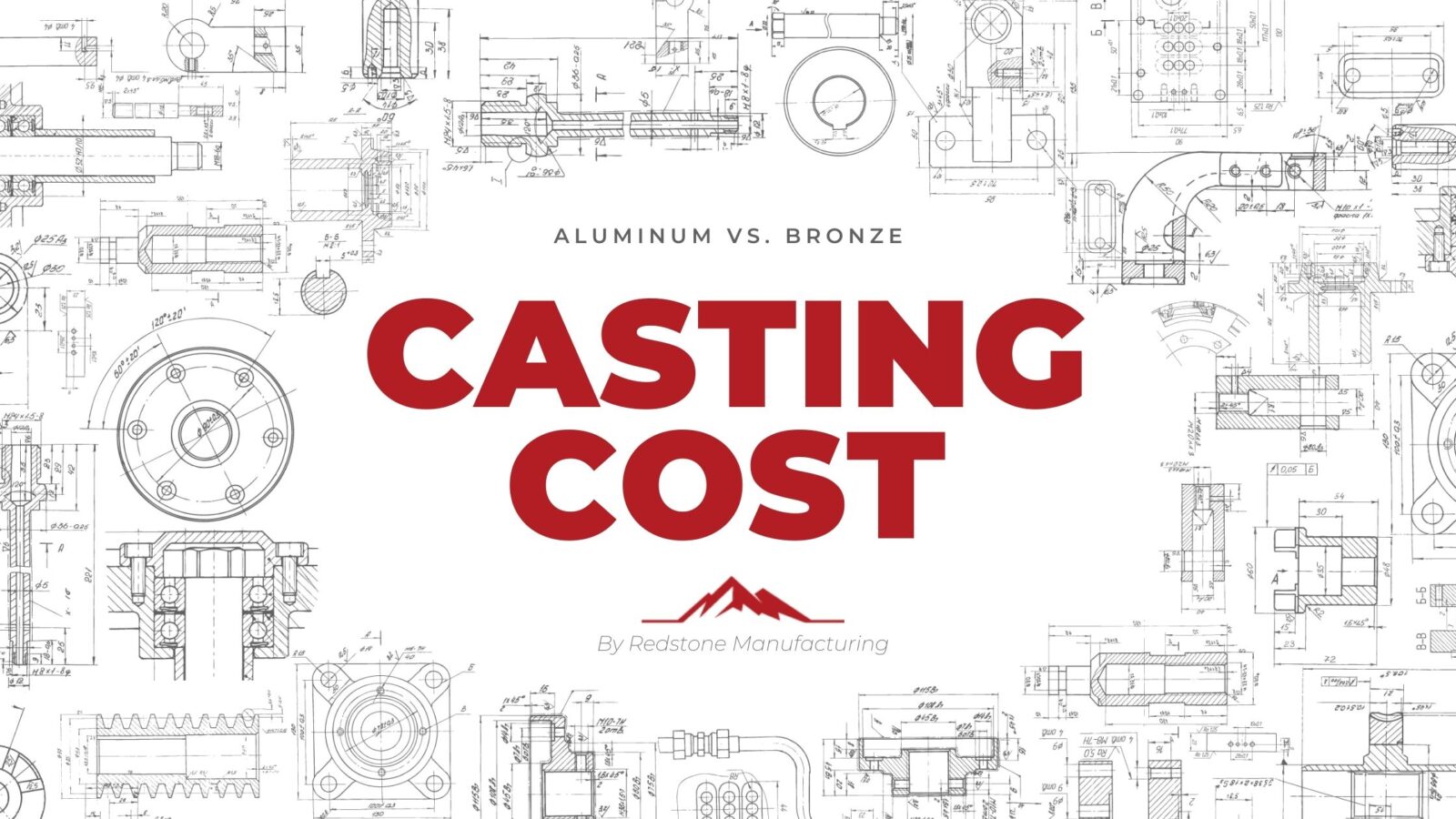
In accuracy casting, 6063 is fit for applications where detailed geometries and high-grade surface finishes are vital. Examples consist of telecommunication rooms, where the alloy's remarkable formability permits streamlined and aesthetically pleasing designs while preserving architectural honesty. Likewise, in the Illumination Solutions market, precision-cast 6063 elements produce sophisticated and effective illumination fixtures that call for elaborate shapes and good thermal performance.
It causes a better surface area finish and far better rust resistance in A360. In addition, the A360 shows premium prolongation, making it perfect for complex and thin-walled components. In accuracy spreading applications, A360 is well-suited for markets such as Consumer Electronics, Telecommunication, and Power Devices. Its boosted fluidness allows for complex, high-precision components like smart device housings and Find Out More interaction gadget housings.
Rumored Buzz on Alcast Company
Its one-of-a-kind homes make A360 a useful option for precision casting in these industries, improving item durability and quality. Light weight aluminum alloy 380, or A380, is a widely made use of spreading alloy with numerous distinctive features. It uses excellent castability, making it an optimal option for accuracy casting. A380 exhibits good fluidness when molten, ensuring detailed and in-depth molds are properly reproduced.
In accuracy casting, light weight aluminum 413 shines in the Consumer Electronic Devices and Power Tools markets. This alloy's remarkable corrosion resistance makes it an outstanding option for exterior applications, ensuring durable, sturdy items in the mentioned sectors.
Alcast Company for Beginners
The aluminum alloy you select will considerably impact both the casting procedure and the properties of the final product. Since of this, you have to make your choice thoroughly and take an educated technique.
Identifying the most suitable light weight aluminum alloy for your application will certainly indicate weighing a wide selection of features. The very first classification addresses alloy qualities that affect the production process.
See This Report about Alcast Company
The alloy you pick for die casting straight impacts several elements of the casting process, like just how simple the alloy is to collaborate with and if it is susceptible to casting issues. Hot fracturing, also referred to as solidification fracturing, is a regular die casting defect for light weight aluminum alloys that can result in inner or surface-level tears or fractures.
Certain aluminum alloys are extra vulnerable to warm fracturing than others, and your selection must consider this. An additional common problem located in the die casting of aluminum is die soldering, which is when the actors adheres to the die walls and makes ejection challenging. It can harm both the actors and the die, so you should search for alloys with high anti-soldering homes.
Rust resistance, which is already a remarkable attribute of aluminum, can vary considerably from alloy to alloy and is a necessary particular to take into consideration relying on the ecological problems your item will certainly be revealed to (aluminum foundry). Put on resistance is an additional property commonly looked for in light weight aluminum items and can separate some alloys
Report this page